ARTIFICIAL INTELLIGENCE IN QUALITY CONTROLS
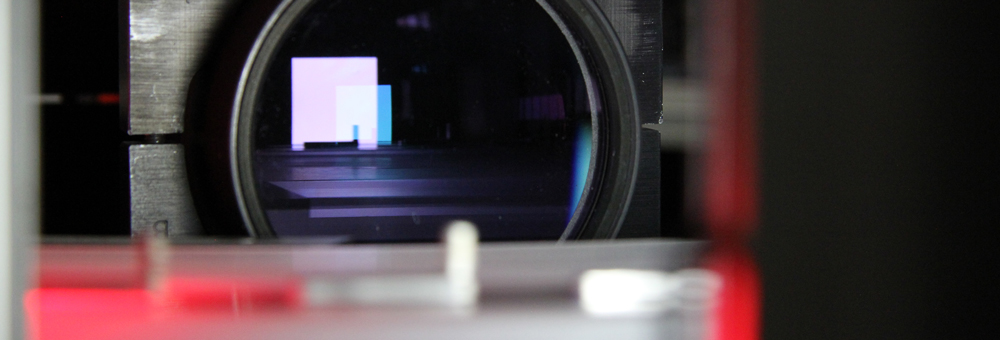
A new industrial revolution triggered by the application of artificial intelligence to automation processes is arriving. Quality Control are amongst the industry sectors that are likely to be more involved with the imminent paradigm shift.
In the late 1970s, Champs was one if the first companies to introduce quality control machines for the mechanical industry with the introduction of the analogic-based artificial vision systems. A few years later the company opened the way by developing computerized control systems and releasing the first programs dedicated to the fastener controls.
Today we are going to trepass a new threshold adding to the digital eyes and the mechanical arms of our machines an 'artificial brain' capable of understand and instruct itself to perform in the best way the task for which it was thought.
The potential benefits the application of machine learning algorithms to automated quality control devices will generate are countless. Artificial Intelligence allows the machine to understand what task it has to perform and to self-define the most effective way to do it. This mechanism is made possible by the application of 'neural networks' or 'super-programs' that can independently develop codes for inspection programs. In other words, the programmer no longer instructs the machine on what and how to control but is A.I. to set parameters and methods to evaluate them. To work properly, however, the system needs to be first instructed: it provides the machine with a set of examples of good parts and then a set of scrap pieces. During this phase, with no further 'human' interference, the neural network will reconstruct a model of the 'standard' piece by analyzing all the captured images and use it as a sample to perform controls on all the parts to sort.
It's easy to understand how in the Q.C. this new technology can make substantial improvements. Control devices will become more and more powerful and easy to handle. Champs is determined to anticipate the market demand by confirming its leadership by introducing shortly the first autonomous machine models. Our R & D department is successfully experimenting with the first prototypes and we can already anticipate what the major benefits of the new systems:
Simplicity: The operator will use the interface only for basic functions such as power-off, machine status control functions, and production report analysis. However, the need to interact at the software level for complex functions such as parameter setting and management, debugging, loading different viewing programs depending on the workpiece will be eliminated.
Versatility : The same machine could be used to control components other than those for which the machine was initially programmed (with the necessary mechanical adaptation adjustments). Through the AI, the machine can 'write' the program independently to perform the controls. Even a basic computer based operator can easily set up and configure the machine for complex operations.
Precision : With the introduction of artificial intelligence systems the accuracy of controls does not vary in terms of measurement accuracy, but increases the potential number of measurements and the degree of interrelation between them. This implies that the selection is even more effective because compliance is not detected on significant parameters but on the workpiece as a whole. There are no 'a priori' key parameters to be met but the machine itself determines which and how many will be more or less binding according to the multiple readings made on the reference samples.
Scalability : Champs is designing new artificial intelligence systems as a software implementation package. Our intention is to make it possible to upgrade all our recent machineries, including those with our latest Albatross 2.0 Vision Software.
In the late 1970s, Champs was one if the first companies to introduce quality control machines for the mechanical industry with the introduction of the analogic-based artificial vision systems. A few years later the company opened the way by developing computerized control systems and releasing the first programs dedicated to the fastener controls.
Today we are going to trepass a new threshold adding to the digital eyes and the mechanical arms of our machines an 'artificial brain' capable of understand and instruct itself to perform in the best way the task for which it was thought.
The potential benefits the application of machine learning algorithms to automated quality control devices will generate are countless. Artificial Intelligence allows the machine to understand what task it has to perform and to self-define the most effective way to do it. This mechanism is made possible by the application of 'neural networks' or 'super-programs' that can independently develop codes for inspection programs. In other words, the programmer no longer instructs the machine on what and how to control but is A.I. to set parameters and methods to evaluate them. To work properly, however, the system needs to be first instructed: it provides the machine with a set of examples of good parts and then a set of scrap pieces. During this phase, with no further 'human' interference, the neural network will reconstruct a model of the 'standard' piece by analyzing all the captured images and use it as a sample to perform controls on all the parts to sort.
It's easy to understand how in the Q.C. this new technology can make substantial improvements. Control devices will become more and more powerful and easy to handle. Champs is determined to anticipate the market demand by confirming its leadership by introducing shortly the first autonomous machine models. Our R & D department is successfully experimenting with the first prototypes and we can already anticipate what the major benefits of the new systems:
Simplicity: The operator will use the interface only for basic functions such as power-off, machine status control functions, and production report analysis. However, the need to interact at the software level for complex functions such as parameter setting and management, debugging, loading different viewing programs depending on the workpiece will be eliminated.
Versatility : The same machine could be used to control components other than those for which the machine was initially programmed (with the necessary mechanical adaptation adjustments). Through the AI, the machine can 'write' the program independently to perform the controls. Even a basic computer based operator can easily set up and configure the machine for complex operations.
Precision : With the introduction of artificial intelligence systems the accuracy of controls does not vary in terms of measurement accuracy, but increases the potential number of measurements and the degree of interrelation between them. This implies that the selection is even more effective because compliance is not detected on significant parameters but on the workpiece as a whole. There are no 'a priori' key parameters to be met but the machine itself determines which and how many will be more or less binding according to the multiple readings made on the reference samples.
Scalability : Champs is designing new artificial intelligence systems as a software implementation package. Our intention is to make it possible to upgrade all our recent machineries, including those with our latest Albatross 2.0 Vision Software.
ARTIFICIAL INTELLIGENCE IN QUALITY CONTROLS FOR FASTENERS